Capacity Utilization Rate
Metric Details & Benchmarking Report Download
KPI Benchmarks : Capacity Utilization Rate
- Benchmark Range
- Benchmark Average
- Benchmark Sample Size (n) 54
* Is High or Low Best: Higher is Better
Capacity Utilization Rate
KPI Details
Manufacturing Capacity Utilization Rate is a vital KPI that measures actual versus potential output within a manufacturing facility or company (i.e., across all facilities managed by the organization), or sometimes within the economy as a whole. On a macroeconomic level, Capacity Utilization Rate is an indicator of economic productivity that speaks to overall demand and how that impacts activity within the manufacturing sector. At the operational level (i.e., within or across a company's manufacturing sites), this KPI can be used to assess the efficiency and allocation of production capacity (e.g., facility A is operating at 85% capacity, while facility B is only at 65% - why is this?). Capacity utilization can also be used at the operational level to determine whether or not existing manufacturing capacity is sufficient to meet forecasted demand (e.g., the facility is currently operating at 70% and we expect a 25% increase in demand; there is an additional 30% capacity available to meet that demand).
KPI Definition
The actual number of units produced (i.e., actual output) by the company, or within a single manufacturing facility/plant, divided by the number of units that could have been produced over the same period of time if the operation was running at full capacity (i.e., potential output), as a percentage.
KPI Best Practices
- Preventative maintenance performed regularly on manufacturing equipment
- High quality raw materials to minimize defective output
- Generate high demand for products
KPI Calculation Instructions Capacity Utilization Rate?
Two numbers are used to calculate this KPI: (1) the actual number of units produced (i.e., actual output) within a single manufacturing facility, or across a selected group of facilities, and (2) the number of units that could have been produced within those facilities over the same time period if they were running at 100% capacity (i.e., potential output). Actual output should be counted as the total number of usable units produced over a given time period within the manufacturing facilities being examined. Potential output should be counted as the number of units that, theoretically, could have been produced within the facilities being examined over the same period of time, based on peak capacity utilization (100% utilization).
KPI Formula :
(Actual Production Output in Units / Potential Production Output in Units) * 100
Related Products
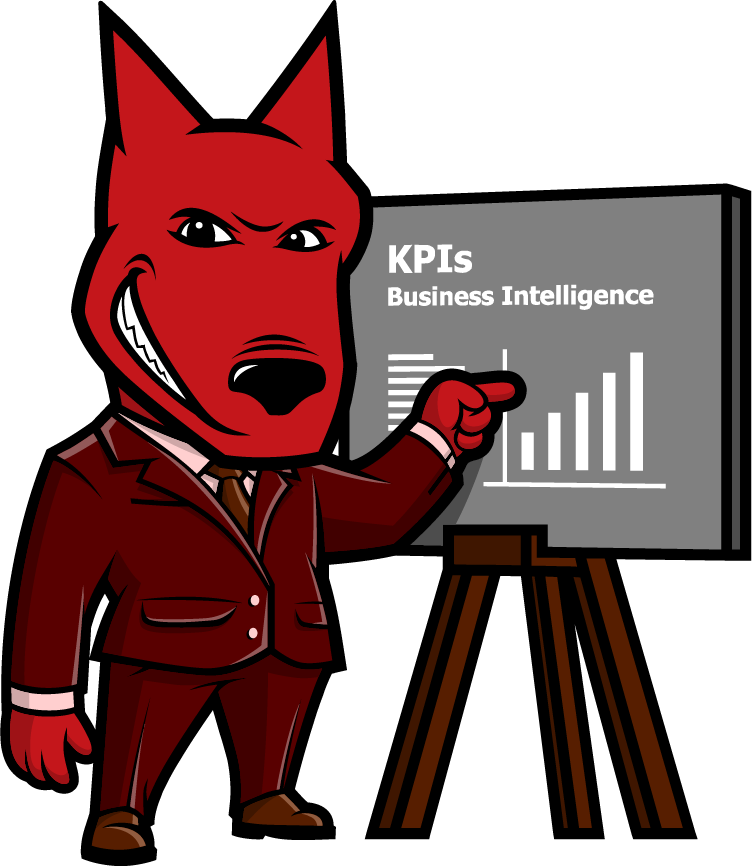
Let us take your KPIs & business intelligence efforts to the top.