Scrap Expense as a Percentage of Plant Revenue
Metric Details & Benchmarking Report Download
KPI Benchmarks : Scrap Expense as a Percentage of Plant Revenue
- Benchmark Range
- Benchmark Average
- Benchmark Sample Size (n) 60
* Is High or Low Best: Lower is Better
Scrap Expense as a Percentage of Plant Revenue
KPI Details
Scrap Expense as a Percentage of Plant Revenue measures the dollar value of scrap produced during the manufacturing process (e.g., units that are scrapped due to errors or defects as well as excess materials that cannot be used) in relation to the total dollar amount of revenue generated by the plant, or production facility, over the same period of time. Excessive expenses incurred by scrapped units is indicative of high rework rates, low quality of raw materials purchased (such low quality materials can cause in increase in rework due or scrap rate due to a high number of defects), poor preventative maintenance practices for plant equipment and machinery, and sub-par production employee training and performance. A high value for this metric not only reduces the opportunity to sell and deliver products to customers on-time, but it also has the potential to expose the company to reputational risks if an item meant to be scrapped is inappropriately sold. This can result in fines, item recalls and customer attrition.
KPI Definition
The dollar value of scrap produced during the manufacturing process (e.g., units that are scrapped due to errors or defects as well as excess materials that cannot be used) divided by the total dollar amount of revenue generated by the plant, or production facility, over the same period of time, as a percentage.
KPI Best Practices
- Use high quality raw materials and components for production runs
- Audit manufacturing process on a regular basis to identify root causes of scrap
- Implement a regular preventative maintenance routine to minimize errors in production
KPI Calculation Instructions Scrap Expense as a Percentage of Plant Revenue?
Two numbers are used to calculate this KPI: (1) the dollar value of scrap produced during the manufacturing process (e.g., units that are scrapped due to errors or defects as well as excess materials that cannot be used), and (2) the total dollar amount of revenue generated by the plant, or production facility, over the same period of time. In this calculation, scrapped materials should be considered to be both excess materials that cannot be used as well as failed assemblies or materials that cannot be repaired or restored cause of errors or product defects. Errors can range from human assembly errors to errors made by manufacturing equipment or machines. Defects are considered to be unintended product issues (products that are lower in quality than expected, contaminated, damaged, etc.) that are caused from improper manufacturing in such a way as to depart from the product’s intended design.
KPI Formula :
(Expense Incurred by Scrapped Units / Plant Revenue Generated) * 100\
Related Products
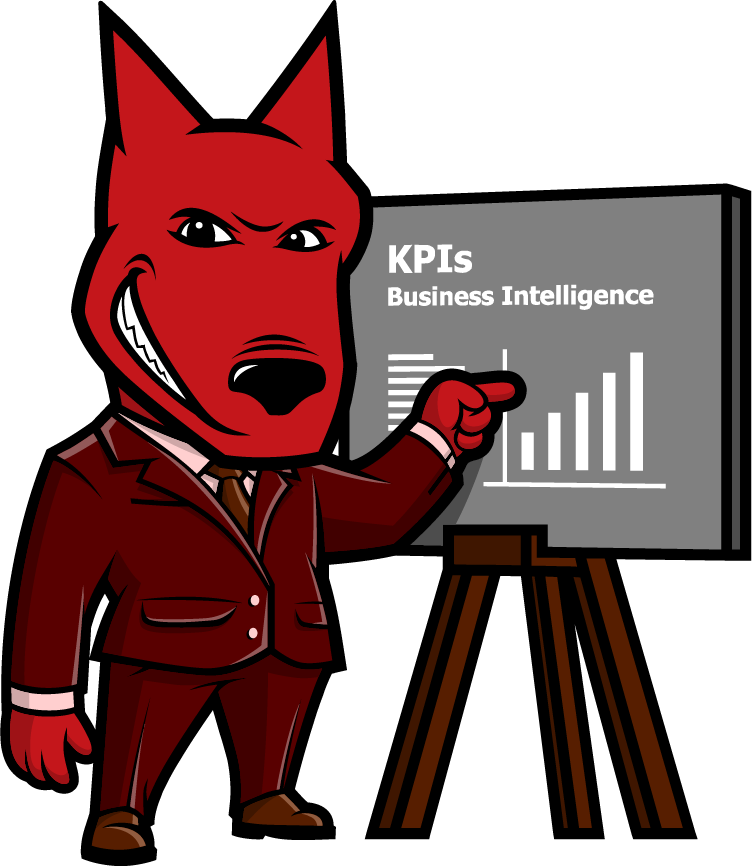
Let us take your KPIs & business intelligence efforts to the top.