Overall Equipment Effectiveness (OEE)
Metric Details & Benchmarking Report Download
KPI Benchmarks : Overall Equipment Effectiveness (OEE)
- Benchmark Range
- Benchmark Average
- Benchmark Sample Size (n) 24
* Is High or Low Best: Higher is Better
Overall Equipment Effectiveness (OEE)
KPI Details
Overall Equipment Effectiveness (OEE) is a vital KPI in Manufacturing & Production that measures the overall performance of the company's production machinery, based on performance, availability and quality. OEE tells managers what percentage of planned production time is truly productive, in terms of producing good units at the optimal cycle time. A relatively low value for this KPI can indicate a number of problems throughout the manufacturing process, such as defective raw materials or final goods (quality), sub-par preventative maintenance controls or inaccurate demand forecasting methods (availability), or slow machine production speed (performance). Some ways tom improve OEE include increased training for maintenance personnel, increased preventative maintenance schedules, replacing old equipment, and improving the quality of raw materials.
KPI Definition
A measurement of production function availability (uptime), performance and quality in a single metric/KPI that assesses the overall efficiency of the entire production operation, expressed as Availability times Performance times Quality.
KPI Best Practices
- Preventative maintenance performed regularly on manufacturing equipment
- Use of lean manufacturing methods such as Six Sigma, MVT, etc.
- Use high quality, tested raw materials during production runs
KPI Calculation Instructions Overall Equipment Effectiveness (OEE)?
Three values are used to calculate this KPI: (1) the number of good units produced during the measurement period (i.e., units that are not scrapped or reworked), (2) the ideal or fastest cycle time it takes to produce one unit of a certain product (measured in minutes, rounded to the nearest tenth), and (3) the total amount of time that manufacturing equipment is scheduled to be in use during the measurement period (measured in minutes, rounded to the nearest tenth). Good units are defined as units that pass inspection and are approved for sale or use as a component in another production run. Do not include time in which the machine is running for testing or other purposes in this calculation. If the ideal cycle time to produce a unit is unknown to Manufacturing managers, they can generate the needed value from the best 2-3 manufacturing days of the past year to estimate an ideal cycle time. Ideal cycle time could also come from the best observed takt time (i.e., time to produce a single unit).
KPI Formula :
((Number of Good Units Produced * Ideal Cycle Time) / Total Amount of Time Equipment is Scheduled for Use) * 100
Related Products
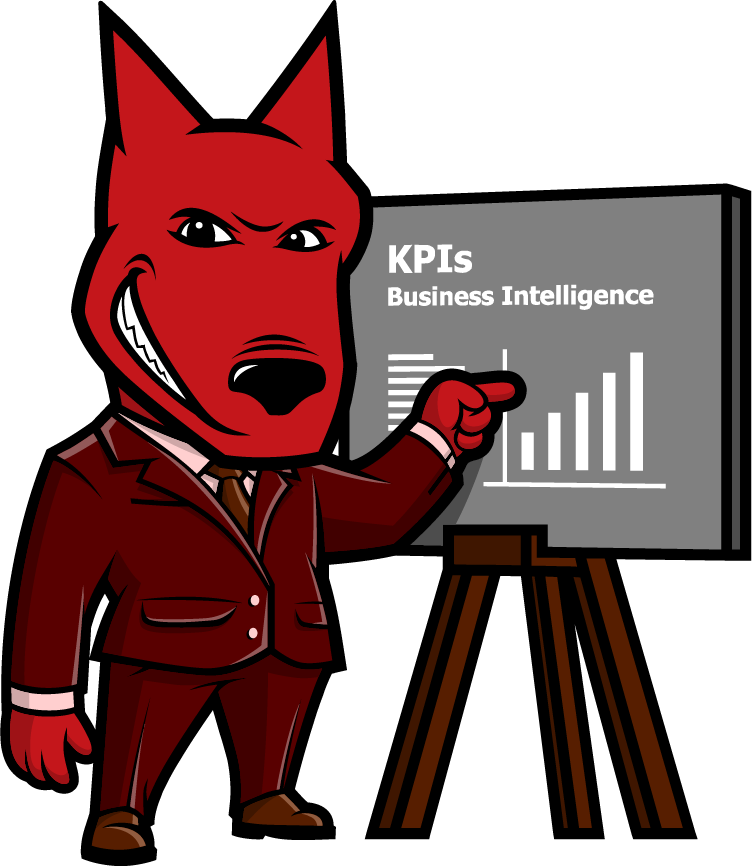
Let us take your KPIs & business intelligence efforts to the top.